Why Is the best
Our straightforward approach simplifies the process,
guiding you through a strategic journey that encompasses consultation, planning, execution, and success.
Great Strategy
Unlock the power of a great strategy tailored to your business goals, driving growth, innovation, and success in today's dynamic marketplace.
Best Promotion
Discover the power of our best-in-class promotion strategies that elevate your brand visibility, captivate your audience, and generate exceptional results.
Effective Marketing
Experience the impact of effective marketing strategies that propel your brand forward, engage your target audience, and drive measurable results.
Unsubscribe
5.7
MLN
TRANSACTIONS
7k
Happy
Clients
7k
ACTIVE
ACCOUNTS
40
COUNTRIES
SERVED
Something special about our agency
What sets our agency apart is our unwavering commitment to excellence and innovation. We strive to go beyond the ordinary, embracing creativity and pushing boundaries to deliver exceptional solutions. Our team of passionate experts brings a unique blend of expertise and fresh perspectives to every project, ensuring that we deliver nothing but the best. With a customer-centric approach, attention to detail, and a deep understanding of industry trends, we create tailored strategies that drive growth and success. Discover the difference of working with an agency that believes in the power of something special, and let us take your business to new heights.
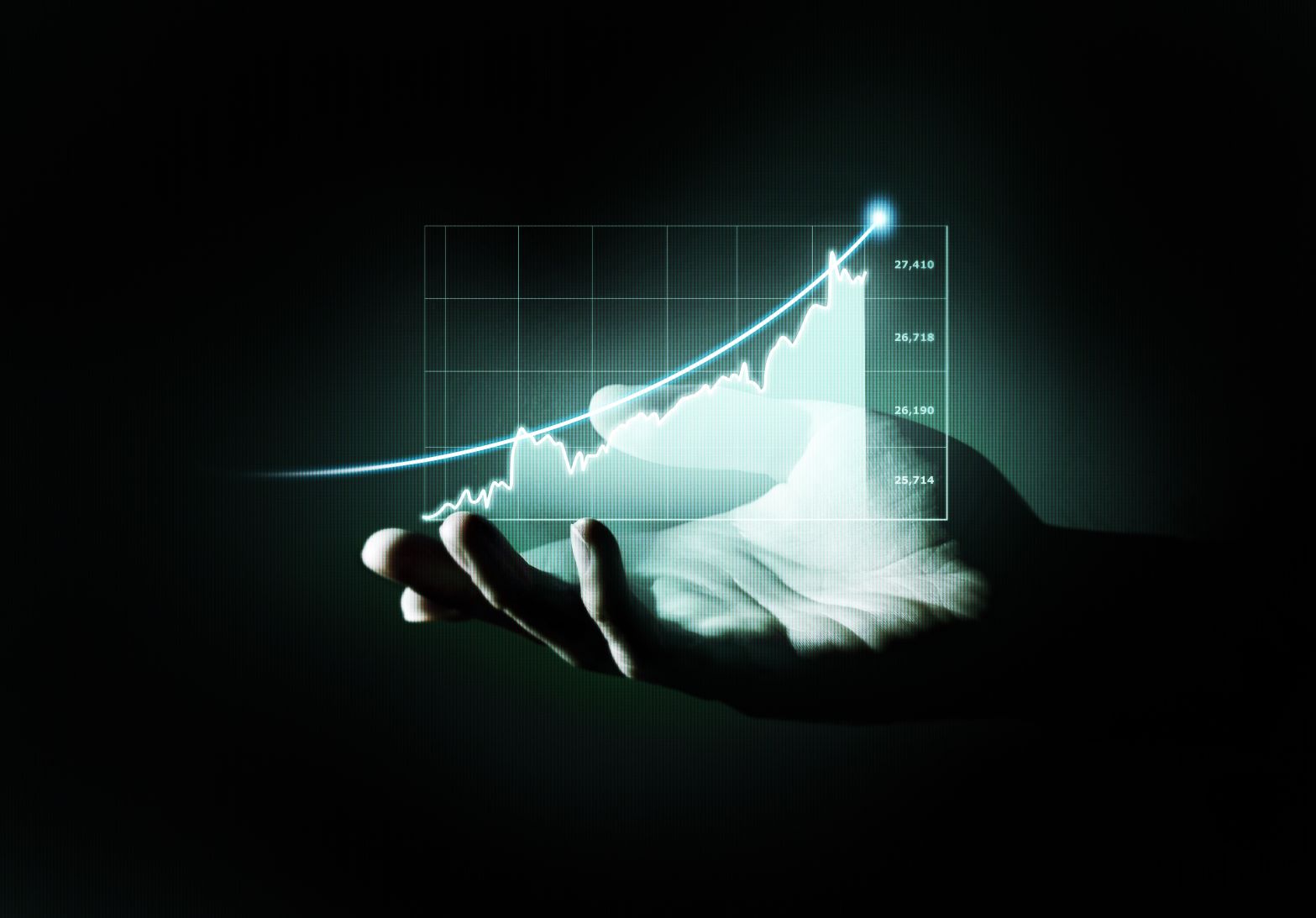